Summary
The AQUADA-GO project develops a methodology for automated, noncontact, near real-time blade damage detection and risk evaluation in a single step using thermography and computer vision without stopping the normal operation of wind turbines. The project will take the AQUADA technology developed in the laboratory of DTU Wind Energy and apply it to operational offshore wind turbines.
The idea for the project originated at DTU Wind and Energy Systems, which has already published scientific articles on the so-called AQUADA technology. The GO in the project title has been added as the partners are now ready to transfer the work from the lab at DTU into the environments in which the industry operates.
The project will offer an innovative, market-ready solution to disrupt the labor-intensive and multi-step blade inspection paradigm. AQUADA-GO will develop and demonstrate software implementation and hardware integration in an all-in-one drone platform for offshore applications. A full-scale prototype system will be tested and demonstrated on RWE-owned offshore wind farms together with the commercial partner Quali Drone and the research partner DTU Wind Energy. The project aims to reduce blade inspection costs by at least 50% and offer a significant contribution to drive down the Levelized cost of energy (LCOE) of wind power by 2-3% over 25-30 years’ project lifetime of offshore wind farms compared to the solutions currently available on the market.
Main activities include (1) Thermal features of blade damages in operational conditions considering environmental effects; (2) Physics-based data-driven computer vision algorithms for automated damage detection and near real-time damage evaluation; (3) Hardware and software integration in an all-in-one drone platform; (4) Onshore testing and offshore demonstration without stopping the normal operation of wind turbines; and (5) Validation of LCOE reduction to verify the economic impact of the developed solutions.
Quali Drone will commercialize the project solution and scale up the business rapidly thanks to the unparalleled competitive advantages of the AQUADA-GO technology and the unique access to hundreds of wind farm sites owned by the project partner RWE Renewables globally.
The AQUADA-GO technology is expected to reduce CO2 emission by 30-50% per turbine inspection compared to commercially available solutions. In total, the AQUADA-GO project is estimated to increase the combined annual turnover of the two involved companies by 125 to 230 million DKK and create 33 to 55 full-time new jobs in 3 to 5 years after project completion.
The project will mature from TRL 5-6 to 7-8 from the beginning of 2023 to the end of 2025.
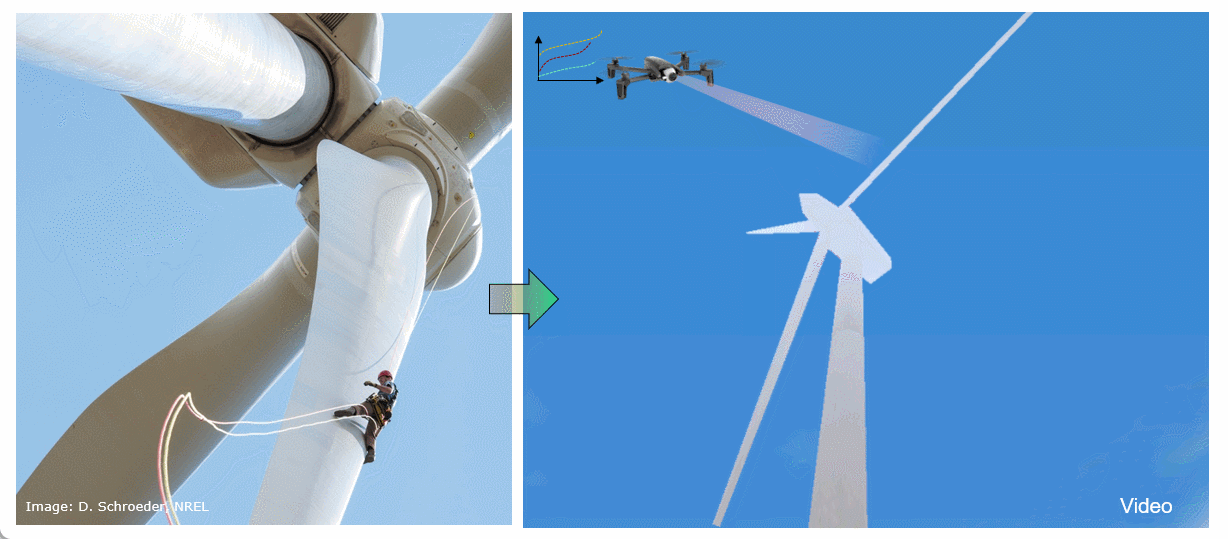